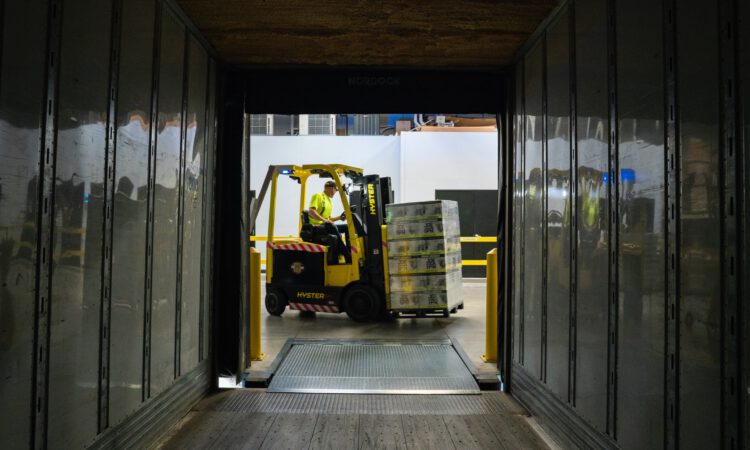
The original features of a warehouse are very well understood. Unlike its predecessors, however, the present day warehouse is an assemblage of extremely evolved automation technologies, which makes it a core the main offer sequence.
These days’s warehouse tasks consist of crossdocking, palletizing, kitting, tagging, and identifying items, along with keeping all of them in most time- and space-efficient manner possible. Because of this, warehouse automation now has an immediate bearing on offer string efficiency.
“The warehouse may be the final frontier for decreasing long-term circulation and logistics prices, ” claims Dan Labell, president, Westfalia Technologies, a warehousing methods planner and implementer headquartered in York, Pa.
Tools for the Trade
Because Westfalia stays in front of the bend on significant warehouse automation styles, a review of the tools it gives to aid companies reduce expense and speed product flows has actually wide implications for warehouses in general.
Robots. Robots play a major role when you look at the materials managing systems Westfalia designs and recommends. The company utilizes articulating arm robots produced by KUKA Robotics Corporation, an international maker of commercial robots, and also by Fuji Yusoki, a number one robotic palletizer maker.
Westfalia programs the robots, but an operator can adjust options and include patterns if they’re not also sophisticated. The robots are set mainly to accomplish palletizing, additionally are widely used to de-palletize layers.
Westfalia additionally utilizes robots to de-palletize and re-palletize levels on its brand new layer storage/retrieval system, which is made to automatically develop “rainbow pallets”—different levels of SKUs for each pallet.
AS/RS Systems. Westfalia manufactures its Automated storing and Retrieval methods (AS/RS), writes a unique computer software, and creates its conveyors and settings.
“Our small, high-density systems save a significant level of floor space, ” Labell notes. “AS/RS systems may be built higher compared to mainstream warehouses, which saves however more living area.”
Besides, AS/RS systems save work, tend to be 99.9-percent accurate, and don’t harm product, Labell claims. Westfalia’s systems can handle around 8, 000-pound plenty of paper also heavy products, also standard weight pallets.
These computer-controlled systems offer access immediately to a significant number of information, which warehouse and logistics managers can retrieve through web links. “We designed our software to be user friendly; even non-computer-literate individuals can discover it quickly, ” Labell notes.
Layer forming palletizers. Layer developing palletizers are often utilized in high-speed applications, as well as in combination with dealing with bags when pattern high quality is very important.
Just how can level forming palletizers match up against robotic palletizers? a level forming palletizer can square each layer before it is removed on the pallet (this applies to bags only). A robot cannot.
A robot is far more versatile, however, as it can manage numerous manufacturing outlines at the same time. Robots may also rapidly pick up numerous cases/bags at some point, but cannot match the speed of the very high-speed outlines often based in the beverage industry, for instance.
“determining between level forming palletizers and robotic palletizers will depend on the application, ” Labell says. “For a warehouse with slow prices and multiple outlines, a robot is probable the better solution. If the rates are very fast, and there is only one line, layer forming can be a better option. The trend, however, is toward robotic palletizing.”
Whether dealing with robots or level creating palletizers, protection is definitely an issue, according to Labell. A layer developing machine or robot cannot access certain areas, like. The robotic palletizing cellular is very dangerous when not guarded correctly with laser security devices or protection walls. Lock-out/tag-out treatments are typically implemented to ensure people aren’t inside a robotic palletizing cellular during operations.
Forklifts. automatic warehouse methods usually use forklifts to load vehicles, but often use counterbalanced vehicles to move item gotten from outdoors, or if perhaps the manufacturing unit is certainly not paired into warehouse. These vehicles are often equipped with RF gear therefore the truck operator can communicate information back into the Warehouse Management program (WMS).
Conveyors. Westfalia’s Air-Chain conveyors use one engine for lengths as much as 100 legs, and need no electric settings to achieve zero-pressure buildup, comparable to a traffic jam concept. Having less settings needed, as well as the proven fact that only a two-horsepower motor will become necessary for up to 20 areas (100 feet), make the conveyors cost effective.
Westfalia makes use of right angle transfers and turntables with regards to desires to transfer pallets in different guidelines while keeping or changing the pallet direction. “when utilizing a turntable, for example, the pallet orientation wont transform, as you tend to be rotating the pallet 90 levels, after that continuing to mention it, ” Labell claims.
Transfer vehicles. Companies make use of transfer automobiles to consolidate numerous pickup or dropoff locations—such as palletizing lines—into a couple of in-feed lines to an AS/RS. A tiny computer system, labeled as the Programmable reasoning Controller (PLC), manages all the equipment. The PLC can be easily set to answer conditions detected by sensing products particularly photoeyes and proximity sensors.
RFID. RFID could be implemented on pallet level, case level, or device level. The medium to long-term trend is have RFID tags on product amount, therefore every product a consumer purchases is tracked. This might be nonetheless relatively cost prohibitive, but most experts agree that unit-level RFID tagging continues to develop.
RFID visitors can be simply built-into any AS/RS to determine pallets in addition to item on a pallet. This data can be used later on due to the fact product moves through the remaining offer sequence.
“RFID is another way to recognize something with no visual mention of the it, ” Labell notes.
Pallets. Plastic pallets continue steadily to grow in appeal. Because they be much more automation friendly, these are typically better to move on conveyers. Though higher priced to shop for than wood pallets, when found in a captive system, synthetic pallets endure more effectively and save money over time. Vinyl pallets may utilized frequently in food programs in which cleanliness is an important problem.