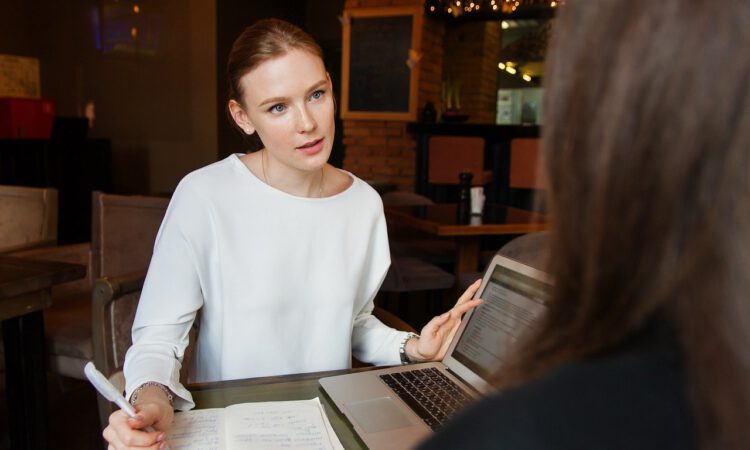
A organization’s inventory control guidelines decide how the business handles the activity of stock under its control. Every organization has an unusual viewpoint on inventory administration that guides just how and exactly why it sets particular guidelines, and an organization's policies may differ based on the type of product managed. Different elements affect inventory control guidelines, like the organization’s administration, the type of product managed and product expense and lead time.
Product Type
The kind of item significantly influences the stock control guidelines assigned to manage the product. Like, services and products with brief rack lives, such as for example perishable meals, require a unique policy than men’s gown tops. Quick shelf life services and products must rotate based on termination time. Though it seems like a first in/first out (FIFO) policy works in this situation, if whenever you want products enter into the warehouse away from termination time sequence, a FIFO policy will neglect to handle the inventory properly. Medical unit producers that produce implantable products need yet another policy than perishable products. Implantable items require a serial number in the external packaging plus the actual item itself. Stock control guidelines that govern the products has to take into consideration the serial range every individual product and keep track of that product by serial quantity through every transfer to and from the warehouse.
Item Expense
A lot of companies employ extra inventory control guidelines for high-value services and products. For example, many warehouses that inventory high priced audio-video equipment keep several of the most high priced equipment secured in cages; just a few associated with warehouse personnel get access to this gear. Alongside getting the services and products caged, many businesses need a signature from authorized workers before high-value services and products move from 1 location within a facility to a different. According to the value of the item, a security guard may accompany the action or transfer.
Lead Time
A major factor that impacts stock control policies is product lead time-the time from bill of an order on time of delivery. Some sectors and items have extraordinarily long lead times. For example, most of a retailer's furnishings no more is manufactured in North Carolina but is made international in China and Vietnam. When furniture was produced in North Carolina, the furnishings retailer could purchase furniture from the provider and have it delivered within two to one month. This short lead time decreased the actual quantity of stock the retailer had a need to carry because he might get more within a reasonably brief notice. When production relocated to China, the lead time increased from two to one month to 90 to 120 days. This entirely altered the retailer's stock policies. He today needs to warehouse more inventory due to the increased lead time. The increased amount of inventory also escalates the workload connected with managing the inventory, such cycle counting, annually physical stock and basic warehouse upkeep.