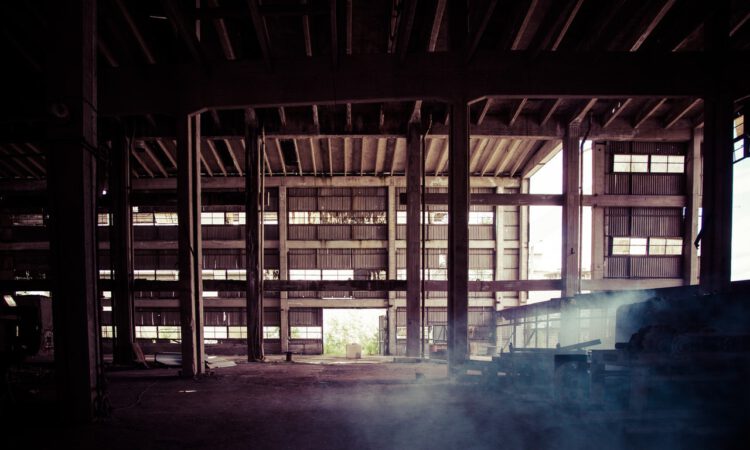
Photo by Pixabay from Pexels
n a small business that will not have accurate inventory records, it is necessary to periodically carry out a total count associated with inventory (known as a physical count). This is done after a month, quarter, or 12 months, to coincide utilizing the end of a reporting period.
Since the after treatment will show, it can take many work to complete an accurate actual stock matter, so businesses have a tendency to limit the range counts finished each year. The measures in the process are the following:
- Purchase count tags. Order an adequate quantity of two-part matter tags the amount of inventory anticipated to be counted. These tags should always be sequentially numbered, in order to be separately tracked included in the counting process.
- Preview inventory. Review the stock a few days prior to the planned inventory matter. If there are missing component figures, or if items be seemingly in a condition which is difficult to count (eg not bagged or boxed), inform the warehouse staff to help make the required modifications.
- Pre-count stock. Go through the inventory a few days beforehand and count any items that can be put into sealed bins. Seal all of them in containers and mark the quantity regarding the sealing tape. This will make the counting task less difficult during the actual count. If a seal is broken, then a counting staff know that they have to re-count the contents of a container.
- Complete data entry. If you will find any staying information entry deals to be completed, do so prior to the actual stock matter begins. Including deals for issuances from the warehouse, returns on warehouse, and transfers between bin areas within the warehouse.
- Inform outside storage locations. If company features any outside storage facilities or third-party places that hold organization stock on consignment, inform them that they should count their stock available as of the state matter day and ahead this information to the warehouse supervisor.
- Freeze warehouse tasks. Stop all deliveries through the warehouse, and also segregate all newly-received products in which they’re not going to be counted. Usually, the inventory documents are going to be in circumstances of flux throughout the stock matter, so will not be totally reliable.
- Instruct count teams. Assemble two-person teams to count the inventory, and instruct all of them within their counting duties. These responsibilities include having anyone count inventory while the other individual scars down the informative data on a count label. One backup regarding the label is attached towards the stock, even though the group retains the other content.
- Problem tags. An inventory clerk issues blocks of matter tags towards matter teams. Each team is responsible for going back a certain numeric array of count tags, set up tags are used. Maintaining control over all matter tags means that lost tags may be examined promptly.
- Assign count areas. Assign a particular array of bins to every matter group. Note these areas with a highlighter on a map regarding the warehouse. The inventory clerk should maintain a master set of which areas of the warehouse have already been counted, and which teams are assigned every single area.
- Amount stock. One individual on each group matters a specific product within a container area, after which each other marks the bin place, item information, component number, volume, and device of measure on a count label. The team affixes the initial backup associated with tag towards the stock item, and maintains the content.
- Verify tags. Upon completion of a matter location, each count group comes back to the inventory clerk, which verifies that all tags had been came back. If there are many warehouse places becoming counted, assign a new location to your count teams and issue them brand-new blocks of matter tags as essential.
- Enter tag information. Enter the home elevators the count tags into an on-line data entry kind. As soon as data entry is finished, print a study showing all label figures entered, sorted by label number, and look for any gaps in numbers. Investigate any numbering gaps discovered. This will make sure all count tags granted were contained in the file.
- Research unusual results. Re-sort the stock report several how to try to find uncommon information, and explore the label entry related to each one.
It might be useful to evaluate this action after each and every matter, to see in the event that treatment should-be changed to compensate for counting issues skilled.