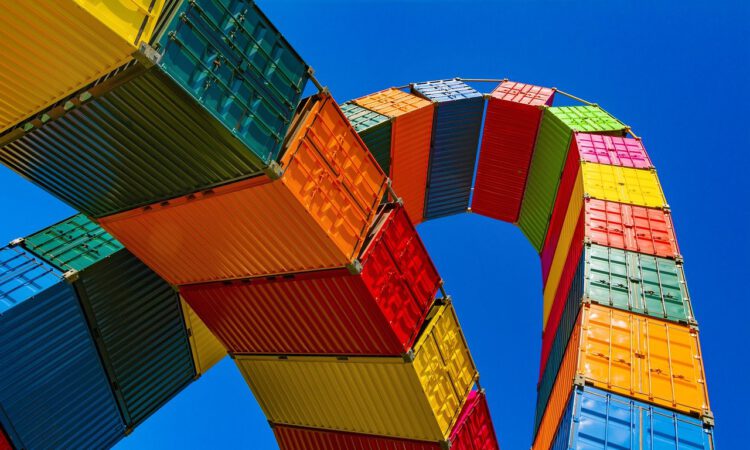
when it is time for you choose and ship e-commerce requests, many smaller businesses tend to follow the same program. The satisfaction process frequently requires printing-out paper pick listings per order, choosing items for just one purchase at the same time, packaging and shipping that order, then moving forward to the next choose number from the imprinted pile.
This program is called discrete choosing and shipping, and is the most common satisfaction technique among online retailers. While discrete fulfillment is easy and simple to adopt, that ease of use comes at a major price in fulfillment effectiveness. You may be choosing and shipping your sales far more rapidly and accurately, leaving you with more time and energy to operate the rest of the company.
Discrete satisfaction, your worst picking and packing opponent
Discrete fulfillment procedures are light on “process” — that’s why many small businesses make do perfectly utilizing it. What you need to do is get a summary of things required for an order, head up to your shop, and begin picking those items. The items enter a box, you type up some shipment configurations, and print-out a label.
But this ease can affect just how rapidly you will be fulfilling your requests. Because you are only choosing one order at the same time, you will find yourself walking towards same products or sections of your store several times in a day. For example, if one item is part of 20 instructions in one day’s queue, then a discrete picker will be walking to that item’s location, selecting it, then moving forward to another item 20 times that day. Likewise, that product could be packed and delivered the same way 20 different occuring times, requiring the employee to kind out almost exactly the same shipment tips and await a label to printing each and every time.
The vacation time taken between products in a shop actually one thing many small business owners concern yourself with. It’s clear — you most likely have larger fish to fry. It really is common for a worker to simply begin with the top of a picking number and work their particular way-down to the base. Because procedure, the picker may be driving things that they want, simply to go back to that item afterwards. These types of little efficiency gaps can add on around a big (and costly) expense over time and work.