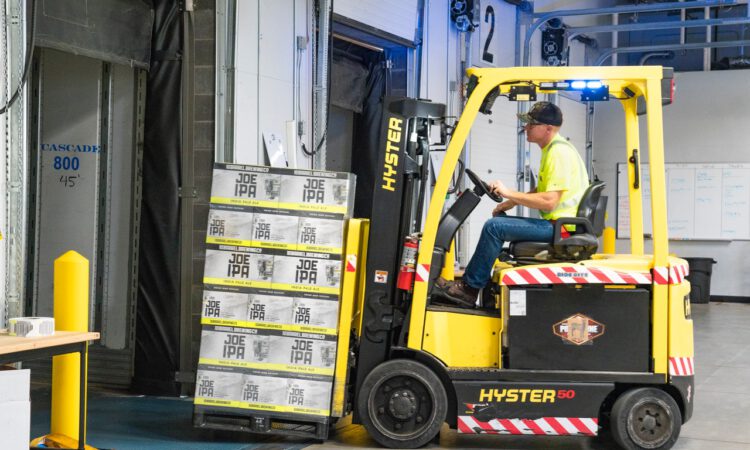
Improving the productivity of a warehouse hasn’t already been even more feasible due to advances in technology. Let’s explore some of the resources available to warehouse managers to increase output in the five warehouse administration processes described below.
1. Collaboration
Correspondence by email is a superb communication tool, however, when it comes to time-sensitive interaction; direct contact is a lot more efficient. Use a number of of this wireless technologies available to raise your output. A vital in selecting technologies is the fact that they must integrate and interact. Whether you decide to communicate through radio, laptop computer or smartphone, spend money on something that most divisions can use consistently. This may provide your warehouse real-time performance and improve output.
2. Receiving
Handle it as soon as. The greater amount of times a product is taken care of plus the more folks mixed up in maneuvering, the greater amount of time and money you will be wasting. Materials must be obtained and kept with complete precision. Your database for stock must certanly be updated as merchandise is obtained.
Having anyone in obtaining checking down received materials from a listing, after that sending materials for stocking, after that sending the list for database updating is certainly not efficient. Incoming processing while the correct Enterprise Resource preparing (ERP) computer software can allow one person to check on in products and record the stock in one action. Those materials are able to be routed towards the correct area within warehouse.
Choose something of barcode scanning or RFID and take the extra handling from your obtaining businesses. This system will even permit the data from incoming deliveries become delivered straight to the buying and AP departments to upgrade the knowledge for prompt payments of invoices.
Just-in-time distribution is a way for maintaining extra stock from increase within facility. The greater material you’ve got simply sitting on shelves, the more cash you have got tied up because inventory.
3. Stock Layout
The organization of the warehouse is very important as it determines exactly how effectively brand new materials are placed away and products tend to be recovered for cargo. Invest in a storage system that fits the requirements of your facility. Your design should be designed based on your unique operations. If specific things are purchased and sent collectively, that is how they ought to be stored. If a numerical system is most effective, after that that is the system to use.
If your materials are kept on pallets, have the correct system positioned for easy pallet accessibility. If you use containers, possess racking system to allow for all of them. The better your product organization and access, the less time you shed in planning orders for cargo.
The critical thing to keep in mind is the fact that employees shouldn’t need certainly to make a few trips around your entire facility to choose purchases for shipment. The greater amount of time staff members invest whilst travelling around within your facility, the greater productivity that you are losing.
4. Choosing procedures
Selecting and loading are another location in which otherwise efficient warehouses can very quickly fail. If incorrect products tend to be pulled, somebody not merely has to recover the appropriate product, but also not the right items needs to be returned to in which they belong.
If your stock is organized and marked with (for instance) SKUs or a different sort of system, your employees is going to be less likely to want to pull the incorrect products for shipments. Aided by the right computer software, you are able to combine pick listings to complete a few instructions and then sort the person products right inside delivery division.
5. Running and Shipping
When it comes to running and delivery, first-in is certainly not first out. Vehicles should be filled inside reverse order. The past items placed in the vehicle will be the very first things unloaded.
GPS methods can help you enhance your loading, routing and deliveries. This final step can help you ensure customer satisfaction. You will be aware in which shipments are if consumers have questions.
Utilize the organization, interaction, storage space and software solutions available to maintain your warehouse functions up to date. These implementations will boost your output, decrease mistakes and improve the important thing for the facility.